Tartalomjegyzék
befektetési öntési folyamat lépései
a befektetési öntés évezredek óta sikeresen hoz létre nettó alakú termékeket különböző formákban. Bár az új anyagok és gyártási technikák bevezetése az elmúlt években bizonyos változásokhoz és fejlesztésekhez vezetett, a befektetési öntési folyamat lépései nagyrészt változatlanok maradtak. (A befektetési öntés előnyeiről itt olvashat).
általában a befektetési öntés, vagy néha elveszett viaszöntésnek is nevezik, a következőkben foglalható össze 8 lépések.
1.lépés – mester minta
a mester mintát viaszból, agyagból, fából, acélból vagy műanyagból készít egy speciális formagyártó vagy szobrászművész a végtermék követelményeinek megfelelően. Ezeket mind a viasz, mind az öntőanyag zsugorodásának figyelembevételével készítik, ezért hívják, “mester minta” a kettős zsugorodási juttatás miatt. Az alábbi 1. ábra egy fából készült mestermintát és öntését mutatja.
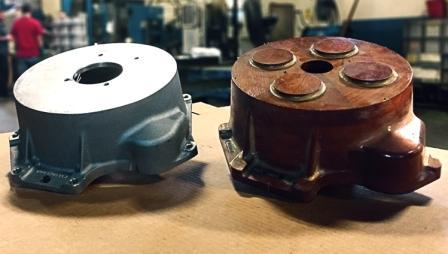
attól függően, hogy a méret, forma és a felhasznált anyag, ez a folyamat eltarthat néhány próba és hiba, hogy a méret és a forma helyes, így ezek a formák drága.
2. lépés-mester die / penész / penész
a penész, ismert, mint a mester meghalni, hogy hozzon létre viasz minták készül, hogy illeszkedjen a mester minta öntés vagy megmunkálás. A szerszámozás és a CNC-megmunkálás technológiai fejlődése lehetővé tette, hogy egy mesterszerszám megmunkálása olyan anyagból, mint az acél és az alumínium, anélkül, hogy szükség lenne mestermintára, amint azt a 2.ábra mutatja.
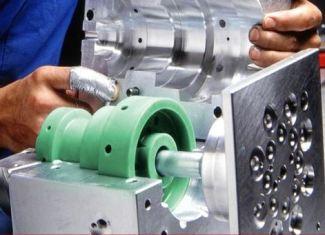
ha a mester minta acélból készül, akkor a mester szerszám közvetlenül az acél mester mintából önthető, alacsonyabb olvadáspontú fém felhasználásával, mint az acél. A szilikon gumi formákat manapság is széles körben használják, mivel egyszerűségük miatt öntőformát közvetlenül a mestermintából öntenek. A szilikon gumi formák ellenállnának az öntési hőmérsékletnek körülbelül 310oc (590of) értékig.
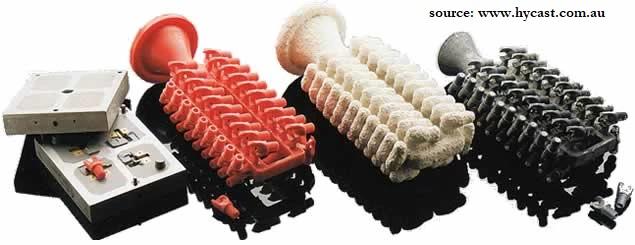
a mestermintát és a mesterszerszámot úgy kell megtervezni, hogy figyelembe vegyék a minta viasz, tűzálló anyag és a fém öntött anyag zsugorodását. Az is jó gyakorlat, hogy a megmunkálás utáni megmunkáláshoz szorosabb tűrési felületeken adjunk hozzá megmunkálási juttatásokat. Egy másik fontos szempont a kétrészes mester meghal vagy formák penész igazítás lokátorok. Az öntőformák kritikus fontosságúak a két fél összehangolásában, hogy pontos alkatrészeket állítsanak elő nagy elválasztó vonalak vagy elválasztó vonalak eltolódása nélkül. (3. ábra)
3. lépés-Minta
a mintákat ezután úgy készítjük el, hogy olvadt viaszt injektálunk vagy öntünk a mester szerszámba, és hagyjuk megkeményedni (4.ábra). Néha bevonatként is használják, ahol a szerszám belső üregfalait viasszal vonják be, hogy üreges mintát kapjanak. Ezt a bevonatot addig ismételjük, amíg a kívánt mintázatvastagságot el nem érjük, általában körülbelül 3 mm (0,12 hüvelyk). Ez utóbbi csak egyszerű alkatrészekre alkalmas. Néha a mintákat megfelelő polimerek és fagyasztott higany felhasználásával is készítik.
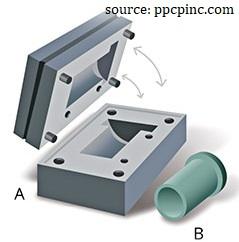
a gyors prototípuskészítés legújabb fejleményei lehetővé tették a minták előállítását közvetlenül egy CAD fájlból, akár mestermintaként, akár viaszmintaként, következésképpen csökkentve a költségeket. A 3D nyomtatási technológiákat, mint például a sztereolitográfiát, a szelektív lézeres szinterezést (SLS), a fused deposition modeling (FDM) és a poli jettinget egyre inkább használják minták létrehozására. Ezek a gyors prototípus-technológiák létrehozásuk során rétegezési technikát alkalmaznak, így a legtöbb esetben utófeldolgozásra van szükség a jó felületminőség biztosítása érdekében.
a magok általában oldható viaszból vagy kerámiából készülnek, ahol az oldható viaszmagokat feloldják az előfeldolgozási mintákból, míg a kerámia magok megmaradnak, és a fémöntvény megszilárdulása után eltávolítják őket.
a tökéletlenségek “üldözésének” nevezett folyamatban, mint például az elválasztó vonalak és a villanások eltávolítása fűtött fém szerszámmal történik, és felszabadító szereket, például szilikon spray-ket is használnak a minta eltávolításának elősegítésére és a minták károsodásának elkerülésére.
4.lépés – Minta összeállítás
a viaszmintákat ezután egy közös viaszrétegre szerelik össze. Sprue egy csatorna, amelyen keresztül olvadt ötvözet elérheti a penész egy befektetés gyűrű után a viasz már megszűnt.
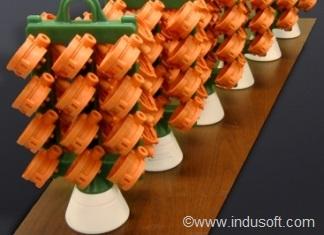
fűtött szerszámok és olvasztott viasz segítségével számos viaszmintát lehet csatolni egy központi sprue és runner rendszerhez, hogy létrehozzanak egy mintafürtöt vagy egy fát. Az alkatrészek méretétől függően akár több száz mintát is össze lehet szerelni egy fára, növelve a termelékenységet. (5. ábra)
a Sprue megtartja a viaszmintát, hogy elkerülje a torzítást az öntési folyamat során, létrehozva egy csatornát az olvadt viasz számára, hogy kiszabaduljon az öntőformából, majd lehetővé tegye az olvadt anyag áramlását az öntőformába.
5.lépés – Bemerítő bevonat
a mintát ezután finomra őrölt tűzálló anyag szuszpenziójába mártják, majd leeresztik, hogy egységes felületi bevonatot hozzanak létre, amelyet “Prime coat” – nak neveznek. Ebben a szakaszban egy nagyon finom részecskeméret letétbe, hogy hozzon létre egy vékony, de nagyon sima réteg befektetési anyag, hogy biztosítsa a sima felület és bonyolult részletes végtermék. Tűzálló anyagként általában nagyon finom szilícium-dioxidot és más kötőanyagokat, köztük vizet, etil-szilikátot és savakat használnak.
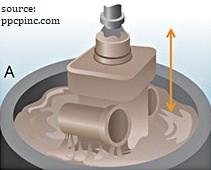
miután a kezdeti réteg megszáradt, a mintát többször mártják és bevonják, hogy növeljék vastagságát a jobb szilárdság érdekében. A mártási folyamat második szakaszát “stukkózásnak” nevezzük, amelyben homok vagy más tűzálló aggregátum esik a nedves felületen a vastagság (5-15 mm ) és az erő növelése érdekében.
néha alternatív módszerként az egyszeres mintás klasztert fejjel lefelé egy áteresztő lombikba helyezik, és folyékony befektetési anyagot öntenek körülötte. A lombikot ezután vibrálják, hogy eltávolítsák a beszorult levegőt, és biztosítsák, hogy a befektetési anyag körülvegye a penészfa minden felületét.
ezt ezután hagyjuk teljesen megszáradni, ami 16-48 órát vehet igénybe. A szárítást vákuum alkalmazásával vagy a környezeti páratartalom minimalizálásával lehet felgyorsítani.
6. lépés-gyantázás és égetés
miután a tűzálló anyag öntőformája teljesen megszáradt és kikeményedett, fejjel lefelé fordítják, és kemencébe vagy speciális célú viaszmentesítő autoklávba helyezik, ahol a viasz megolvadhat és kifogyhat (7.ábra), és az azt követő maradék elpárolog. (Ezek a szimulációk megmutatják, hogyan működnek a speciális viaszmentesítő gépek video 1 vagy videó 2)

a mintaviasz eltávolítása a formából a befektetési öntési folyamat fontos szakasza, és ha helytelenül hajtják végre, csökkenti a tétel hozamát. A viaszmentesítés a héj repedésének egyik fő oka is. A héjrepedés az egyetlen leggyakoribb befektetési öntési hiba.
alapvetően két fő módszer létezik a viaszmentesítésre, flash tűz vagy autokláv (gőz). A gőz autoklávok az előnyben részesített választás egyenletes melegítésük miatt, amely csökkentené az anyag terhelését.
a formát melegítjük (90oC–175oc), és néhány órán át (kb. 4-12 órán át) fordított helyzetben tartjuk, hogy a viasz megolvadjon és kifogyjon. A mintaviaszt általában visszanyerik és újrahasznosítják. Ezután melegítjük és magas hőmérsékleten tartjuk (650oC–1095oc) néhány órán keresztül (3-6 óra), hogy elűzzük a kristályosodás vizét és leégessük a maradék viaszt. Az időtartam és a hőmérséklet függ a fém öntött anyag.
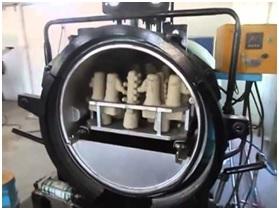
a legtöbb héjhiba a viaszmentesítési szakaszban fordul elő, mivel az alkalmazott viaszok hőtágulási együtthatója nagyobb, mint a tűzálló anyagé. Ezért a viasz jobban kitágul, mint a befektetési anyag, és esetleges stressztörést okoz a penészen. Ennek a hatásnak a csökkentése érdekében a viasz gyorsan felmelegíthető, így a külső viasz gyorsabban megolvad, és hagyja, hogy a maradék viasz kibővüljön anélkül, hogy megterhelné a formát. A 8. ábrán látható autoklávok szintén használatosak e hatás hőcsökkentésére, mivel a fűtési ciklusok egyenletesebbek és pontosabban szabályozhatók.
7. lépés-előmelegítés& öntés
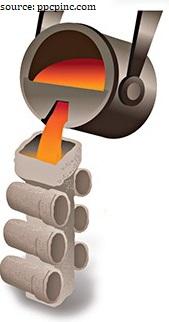
a formát ezután előmelegítik az öntés előkészítése céljából. Az előmelegítés lehetővé teszi, hogy a fém hosszabb ideig maradjon olvadt állapotban, így jobban kitöltheti az összes penészrészletet és növelheti a méretpontosságot. Ha a formát hűlni hagyják, a talált repedések kerámia iszappal vagy speciális cementtel javíthatók. A penészfűtés jobb méretszabályozást is biztosít, mivel a forma és a fém hűtés közben összezsugorodhat.
3000oc-ig olvadt fémet öntünk az üreges formába, majd hagyjuk kihűlni. Míg a gravitációs öntés a legegyszerűbb, más módszerek is alkalmazhatók a forma teljes kitöltésének biztosítására. Komplex, vékony szakaszok esetén a penész kitöltését pozitív Légnyomás, dönthető öntés, vákuumöntés vagy centrifugális öntési folyamat segítheti.
8. lépés-Knockout & utófeldolgozás
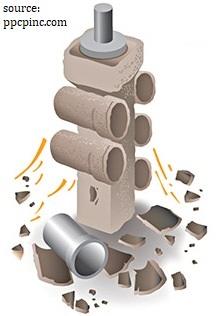
miután a fém megszilárdult, technikák, mint például a mechanikus forgácsolás, kalapálás, rezgő, nagynyomású víz jetting és a Média robbantási használják megtörni a penész, és távolítsa el a fémöntvény. Ezután az egyes öntvényeket levágják, és eltávolítják a felesleges fémet. A sprue-t levágják és a legtöbb esetben újra felhasználják. Az alkatrészt ezután a végtermék követelményeinek megfelelően utómunkálják, például utómegmunkálás, hőkezelés, felületkezelések, festés stb.
referenciák és ajánlott olvasmányok
- Kalpakjian, S., & Schmid, Sr (2009). Gyártástechnika & technológia (hatodik Szerk.). London: Pearson.
- Fekete, J. T, & Kohser, S. Ronald. (2012). Anyagok & feldolgozás a gyártásban (tizenegyedik Szerk.). London: John Wiley.
- Beeley, Peter, (2009). Öntödei technológia (második Szerk.). Oxford: Butterworth-Heinemann.
- Groover, P. Mikell, (2010). A modern gyártás alapjai (negyedik Szerk.). Oxford: John Wiley.