Inhaltsverzeichnis
Feinguss-Prozessschritte
Feinguss erzeugt seit Tausenden von Jahren erfolgreich netznahe Produkte in verschiedenen Formen. Obwohl die Einführung neuer Materialien und Fertigungstechniken in den letzten Jahren zu einigen Änderungen und Verbesserungen geführt hat, sind die Feingussprozessschritte weitgehend unverändert geblieben. (Sie können hier über die Vorteile der Verwendung von Feinguss lesen).
Im Allgemeinen kann Feinguss oder manchmal auch als Wachsausschmelzguss bezeichnet in die folgenden 8 Schritte zusammengefasst werden.
Schritt 1 – Mastermuster
Ein Mastermuster wird aus Wachs, Ton, Holz, Stahl oder Kunststoff von einem spezialisierten Formenbauer oder Bildhauer gemäß den Anforderungen des Endprodukts erstellt. Diese werden unter Berücksichtigung der Schrumpfung von Wachs und Gussmaterial hergestellt, daher wird es „Master Pattern“ genannt, um eine doppelte Schrumpfungszulage zu haben. Abbildung 1 unten zeigt ein hölzernes Mastermuster und seinen Guss.
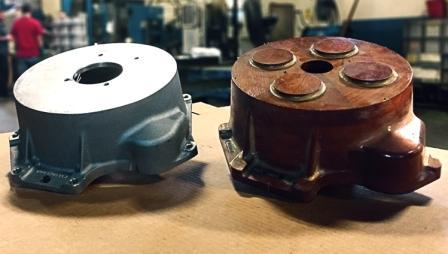
Abhängig von der Größe, der Form und dem verwendeten Material kann dieser Prozess einige Versuche und Irrtümer erfordern, um die richtige Größe und Form zu erhalten, was diese Formen teuer macht.
Schritt 2 – Master die / Mould / Mold
Eine Form, die als Master Die zur Erstellung von Wachsmustern bekannt ist, wird entweder durch Gießen oder Bearbeiten an das Master-Muster angepasst. Der technologische Fortschritt bei der Werkzeug- und CNC-Bearbeitung hat die Bearbeitung eines Hauptwerkzeugs aus einem Material wie Stahl und Aluminium ermöglicht, ohne dass ein Hauptmuster erforderlich ist, wie in Abbildung 2 gezeigt.
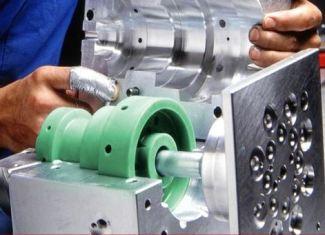
Wenn das Master-Muster aus Stahl besteht, kann das Master-Werkzeug direkt aus dem Stahl-Master-Muster mit Metall mit einem niedrigeren Schmelzpunkt als Stahl gegossen werden. Silikonkautschukformen werden heutzutage auch häufig verwendet, da sie einfach zu verwenden sind, um eine Form direkt aus einem Mastermuster zu gießen. Silikonkautschukformen würden der Castingtemperatur bis zu ungefähr 310oC (590oF) widerstehen.
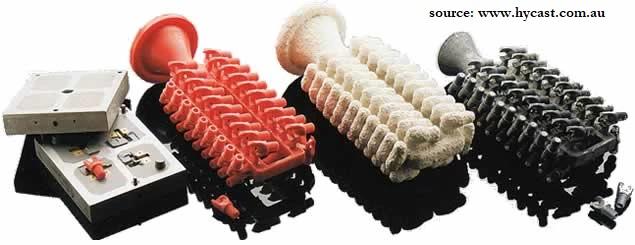
Das Vorlagenmuster und die Vorlagenmatrize müssen unter Berücksichtigung des Schrumpfens von Vorlagenwachs, feuerfestem Material und Metallgussmaterial ausgelegt werden. Es ist auch eine gute Praxis, Bearbeitungszugaben für die Nachbearbeitung auf engeren Toleranzflächen hinzuzufügen. Ein weiterer wichtiger Aspekt von zweiteiligen Matrizen oder Formen sind Formausrichtungsortungsgeräte. Mould Locators sind entscheidend für die Ausrichtung der beiden Hälften, um genaue Teile ohne große Trennlinien oder Trennlinienverschiebungen herzustellen. (Abbildung 3)
Schritt 3 – Muster
Die Muster werden dann hergestellt, indem geschmolzenes Wachs in die Vorlagenmatrize injiziert oder gegossen wird und diese aushärten kann (Abbildung 4). Manchmal wird es auch als Beschichtung verwendet, bei der die Innenhohlraumwände der Matrize mit Wachs beschichtet werden, um ein hohles Muster zu erhalten. Diese Beschichtung wird wiederholt, bis die gewünschte Musterdicke in der Regel etwa 3 mm (0,12 in) erreicht ist. Letzteres nur für einfache Teile geeignet. Manchmal werden Muster auch mit geeigneten Polymeren und gefrorenem Quecksilber hergestellt.
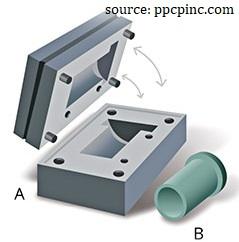
Die jüngsten Fortschritte im Rapid Prototyping haben die Herstellung von Mustern direkt aus einer CAD-Datei ermöglicht, entweder als Mastermuster oder als Wachsmuster, wodurch die Kosten gesenkt werden. 3D-Drucktechnologien wie Stereolithographie, selektives Lasersintern (SLS), Fused Deposition Modelling (FDM) und Poly Jetting werden zunehmend zur Erzeugung von Mustern eingesetzt. Diese Rapid-Prototyping-Technologien verwenden bei ihrer Erstellung eine Schichttechnik, so dass in den meisten Fällen eine Nachbearbeitung erforderlich ist, um eine gute Oberflächengüte zu gewährleisten.
Kerne werden im Allgemeinen aus löslichem Wachs oder Keramik hergestellt, wobei lösliche Wachskerne vor der Verarbeitung aus den Mustern gelöst werden, während die Keramikkerne verbleiben und nach dem Erstarren des Metallgusses entfernt werden.
In einem Prozess namens „Chasing“ werden Unvollkommenheiten wie Trennlinien und Flashings mit einem beheizten Metallwerkzeug entfernt und Trennmittel wie Silikonsprays werden ebenfalls verwendet, um das Entfernen von Mustern zu unterstützen und Schäden an den Mustern zu vermeiden.
Schritt 4 – Mustermontage
Die Wachsmuster werden dann auf einen gemeinsamen Wachsanguss montiert. Anguss ist ein Kanal, durch den geschmolzene Legierung die Form in einem Investitionsring erreichen kann, nachdem das Wachs entfernt wurde.
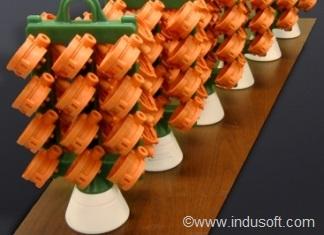
Mit beheizten Werkzeugen und geschmolzenem Wachs können mehrere Wachsmuster an einem zentralen Anguss- und Läufersystem befestigt werden, um einen Mustercluster oder einen Baum zu erstellen. Abhängig von der Größe der Teile können bis zu mehrere hundert Muster zu einem Baum zusammengebaut werden, was die Produktivität erhöht. (Abbildung 5)
Anguss hält das Wachsmuster, um Verzerrungen während des Gießprozesses zu vermeiden, wodurch ein Kanal für das geschmolzene Wachs geschaffen wird, um aus der Form zu entweichen und dann das geschmolzene Material in die Form fließen zu lassen.
Schritt 5 – Tauchbeschichtung
Das Muster wird dann in eine Aufschlämmung aus fein gemahlenem feuerfestem Material getaucht und dann abgelassen, um eine gleichmäßige Oberflächenbeschichtung zu erzeugen, die als „Grundierung“ bezeichnet wird. Während dieser Phase wird eine sehr feine Partikelgröße abgeschieden, um eine dünne, aber sehr glatte Schicht des Einbettmaterials zu erzeugen, um eine glatte Oberfläche und ein kompliziertes detailliertes Endprodukt zu gewährleisten. Sehr feine Kieselsäure und andere Bindemittel, einschließlich Wasser, Ethylsilikat und Säuren, werden üblicherweise als feuerfeste Materialien verwendet.
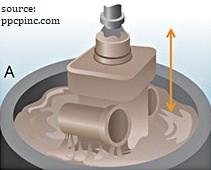
Nachdem die Anfangsschicht getrocknet ist, wird das Muster wiederholt getaucht und beschichtet, um seine Dicke für eine bessere Festigkeit zu erhöhen. Diese zweite Stufe des Tauchprozesses wird als „Stuckieren“ bezeichnet, bei dem Sand oder andere feuerfeste Zuschlagstoffe über die nasse Oberfläche geregnet werden, um die Dicke (5 bis 15 mm ) und Festigkeit zu erhöhen.
Manchmal wird als alternatives Verfahren der einfach getauchte Mustercluster verkehrt herum in einen durchlässigen Kolben eingeführt und mit flüssigem Einbettmaterial umgossen. Der Kolben wird dann vibriert, um eingeschlossene Luft zu entfernen und sicherzustellen, dass das Einbettmaterial alle Oberflächen des Formenbaums umgibt.
Dieser wird dann vollständig trocknen gelassen, was zwischen 16 und 48 Stunden dauern kann. Die Trocknung kann durch Anlegen eines Vakuums oder Minimierung der Umgebungsfeuchtigkeit beschleunigt werden.
Schritt 6 – Entwachsen und Brennen
Sobald die feuerfeste Materialform vollständig getrocknet und ausgehärtet ist, werden sie auf den Kopf gestellt und in einen Ofen oder einen speziellen Entwachsungsautoklaven gestellt, wo das Wachs schmelzen und auslaufen kann (Abbildung 7) und alle nachfolgenden Rückstände verdampfen. (Diese Simulationen zeigen, wie spezialisierte Entwachsungsmaschinen funktionieren Video 1 oder Video 2)

Das Entfernen von Musterwachs aus der Form ist ein wichtiger Schritt im Feingussprozess und verringert bei falscher Durchführung die Chargenausbeute. Das Entwachsen ist auch einer der Hauptgründe für Schalenrisse. Shell Cracking ist der häufigste Defekt beim Feinguss.
Grundsätzlich gibt es zwei Hauptmethoden zum Entwachsen, Flammfeuer oder Autoklav (Dampf). Dampfautoklaven sind die bevorzugte Wahl wegen ihrer gleichmäßigen Heizung, die den Druck auf dem Material verringern würde.
Die Form wird erhitzt (90oC–175oC) und einige Stunden (ca. 4 – 12 Stunden) in umgekehrter Position gehalten, damit das Wachs schmelzen und auslaufen kann. Musterwachs wird normalerweise zurückgewonnen und recycelt. Dann wird es erhitzt und bei einer erhöhten Temperatur (650oC–1095oC) für einige Stunden (3-6 Stunden) gehalten, um das Kristallwasser abzutreiben und jegliches Restwachs abzubrennen. Die Dauer und die Temperaturen hängen vom metallischen Gussmaterial ab.
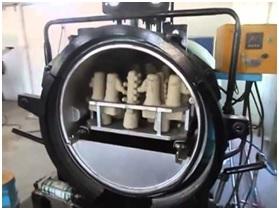
Die meisten Schalenausfälle treten während der Entwachsungsphase auf, da die verwendeten Wachse einen größeren Wärmeausdehnungskoeffizienten aufweisen als das feuerfeste Material. Wachs dehnt sich daher stärker aus als das Einbettmaterial und führt zu einem möglichen Spannungsbruch der Form. Um diesen Effekt zu reduzieren, kann das Wachs schnell erhitzt werden, so dass das äußere Wachs schneller schmilzt und das verbleibende Wachs sich ausdehnen kann, ohne die Form zu belasten. Autoklaven, die in Abbildung 8 gezeigt werden, werden auch verwendet, um diesen Effekt zu verringern, da die Heizzyklen gleichmäßiger und genauer gesteuert werden können.
Schritt 7 -Vorheizen& Gießen
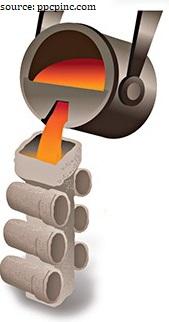
Die Form wird dann zur Vorbereitung des Gießens vorgewärmt. Durch das Vorwärmen bleibt das Metall länger im geschmolzenen Zustand, so dass es alle Formdetails besser ausfüllen und die Maßgenauigkeit erhöhen kann. Wenn die Form abkühlen gelassen wird, können alle gefundenen Risse mit Keramikschlamm oder Spezialzement repariert werden. Formheizung gibt auch bessere Maßkontrolle, weil die Form und das Metall zusammen während des Abkühlens schrumpfen können.
Geschmolzenes Metall bis 3000oC wird in die Hohlform gegossen und dann abkühlen gelassen. Während das Schwerkraftgießen am einfachsten ist, können andere Methoden verwendet werden, um eine vollständige Füllung der Form sicherzustellen. Bei komplexen Dünnschnitten kann die Formfüllung durch Überdruck, Kippguss, Vakuumguss oder Schleudergussverfahren unterstützt werden.
Schritt 8 – Knockout & Nachbearbeitung
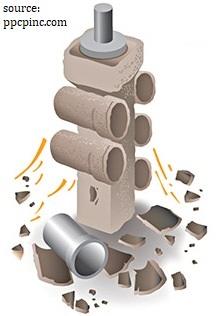
Nach dem Erstarren des Metalls werden Techniken wie mechanisches Abplatzen, Hämmern, Vibrieren, Hochdruckwasserstrahlen und Medienstrahlen verwendet, um die Form zu brechen und den Metallguss zu entfernen. Dann werden einzelne Gussteile weggeschnitten und überschüssiges Metall entfernt. Der Anguss wird abgeschnitten und in den meisten Fällen wiederverwendet. Das Teil wird dann gemäß der Endproduktanforderung wie Nachbearbeitung, Wärmebehandlung, Oberflächenbehandlungen, Lackieren usw. nachbearbeitet.
Referenzen und empfohlene Lektüre
- Kalpakjian, S., & Schmid, S. R. (2009). Fertigungstechnik & Technologie (Sechste Aufl.). In: Pearson.
- Schwarz, J. T., & Kohser, S. Ronald. (2012). Materialien & Verarbeitung in der Fertigung (Elfte Aufl.). London: John Wiley.
- Beeley, Peter, (2009). Gießereitechnik (Second ed.). Oxford: Butterworth-Heinemann.
- Groover, P. Mikell, (2010). Grundlagen der modernen Fertigung (Vierte Aufl.). Oxford: John Wiley.