Tabla de Contenidos
Pasos del proceso de fundición de inversión
La fundición de inversión ha estado creando productos de forma casi neta con éxito en varias formas durante miles de años. Aunque la introducción de nuevos materiales y técnicas de fabricación en los últimos años ha llevado a algunos cambios y mejoras, los pasos del proceso de fundición de inversión se han mantenido en gran medida sin cambios. (Puede leer sobre las ventajas de usar fundición de inversión aquí).
En general, la fundición de inversión o, a veces, la fundición a la cera perdida se puede resumir en los siguientes 8 pasos.
Paso 1-Patrón maestro
Un patrón maestro se crea a partir de cera, arcilla, madera, acero o plástico por un fabricante de moldes especializado o un artista de escultura según los requisitos del producto final. Estos se hacen teniendo en cuenta la contracción del material de cera y de fundición, por lo tanto, se llama «patrón maestro» para tener doble asignación de contracción. La Figura 1 a continuación muestra un patrón maestro de madera y su fundición.
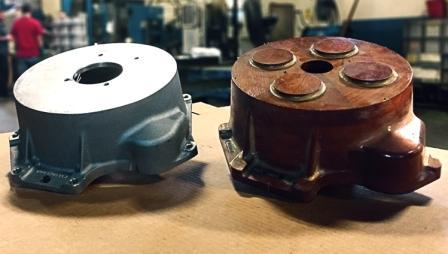
Dependiendo del tamaño, la forma y el material utilizado, este proceso puede requerir un poco de prueba y error para obtener el tamaño y la forma correctos, por lo que estos moldes son caros.
Paso 2: Matriz maestra / Molde / Molde
Un molde, conocido como matriz maestra para crear patrones de cera, se fabrica para adaptarse al patrón maestro, ya sea mediante fundición o mecanizado. El avance de la tecnología en herramientas y mecanizado CNC ha permitido mecanizar una matriz maestra a partir de un material como acero y aluminio sin la necesidad de un patrón maestro, como se muestra en la figura 2.
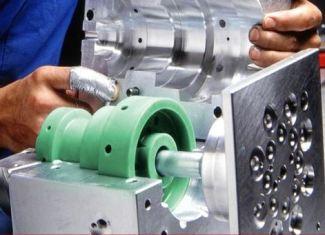
Si el patrón maestro está hecho de acero, la matriz maestra se puede fundir directamente desde el patrón maestro de acero utilizando metal con un punto de fusión más bajo que el acero. Los moldes de caucho de silicona también se utilizan ampliamente en estos días debido a su simplicidad de uso para fundir un molde directamente desde un patrón maestro. Los moldes de caucho de silicona soportarían una temperatura de fundición de hasta aproximadamente 310oC (590oF).
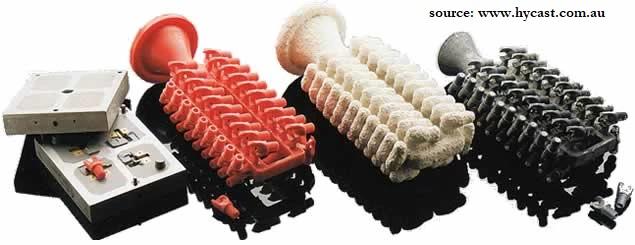
El patrón maestro y la matriz maestra deben diseñarse teniendo en cuenta la contracción de la cera del patrón, el material refractario y el material fundido metálico. También es una buena práctica agregar márgenes de mecanizado para el post mecanizado en superficies de tolerancia más estrechas. Otro aspecto importante de las matrices o moldes maestros de dos partes son los localizadores de alineación de moldes. Los localizadores de moldes son críticos para alinear las dos mitades para producir piezas precisas sin grandes líneas de separación o cambios de línea de separación. (Figura 3)
Paso 3-Patrón
Los patrones se hacen inyectando o vertiendo cera fundida en la matriz maestra y permitiendo que se endurezca (Figura 4). A veces también se usa como revestimiento donde las paredes interiores de la cavidad de la matriz están recubiertas con cera para obtener un patrón hueco. Este recubrimiento se repite hasta que se alcanza el espesor de patrón deseado, por lo general, aproximadamente 3 mm (0,12 pulg.). Este último es adecuado solo para piezas simples. A veces, los patrones también se hacen utilizando polímeros adecuados y mercurio congelado.
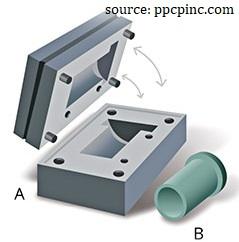
Los recientes avances en la creación rápida de prototipos han hecho posible la producción de patrones directamente a partir de un archivo CAD, ya sea como patrón maestro o como patrones de cera, lo que reduce el costo. Las tecnologías de impresión 3D, como la estereolitografía, la sinterización selectiva por láser (SLS), el modelado por deposición fundida (FDM) y la inyección de polietileno, se utilizan cada vez más para crear patrones. Estas tecnologías de creación rápida de prototipos utilizan una técnica de capas en su creación, por lo que en la mayoría de los casos se requiere un procesamiento posterior para garantizar un buen acabado de la superficie.
Los núcleos generalmente están hechos de cera soluble o cerámica, donde los núcleos de cera soluble se disuelven de los patrones de preprocesamiento, mientras que los núcleos de cerámica permanecen y se eliminan después de la solidificación de la fundición de metal.
En un proceso llamado «Persecución» de imperfecciones, como líneas de separación y tapajuntas, se eliminan utilizando una herramienta metálica calentada y agentes desmoldeantes, como aerosoles de silicona, para ayudar a eliminar los patrones y evitar cualquier daño a los patrones.
Paso 4-Ensamblaje de patrones
Los patrones de cera se ensamblan en un bebedero de cera común. El bebedero es un canal a través del cual la aleación fundida puede llegar al molde en un anillo de inversión después de eliminar la cera.
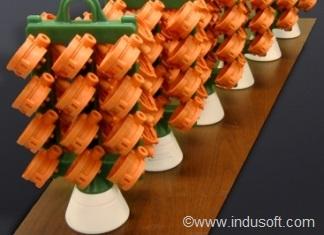
Con herramientas calentadas y cera derretida, se pueden unir varios patrones de cera a un sistema central de bebedero y corredor para crear un grupo de patrones o un árbol. Dependiendo del tamaño de las piezas, se pueden ensamblar hasta varios cientos de patrones en un árbol, lo que aumenta la productividad. (Figura 5)
El bebedero mantendrá el patrón de cera para evitar distorsiones durante el proceso de fundición, creando un canal para que la cera fundida escape del molde y luego permitiendo que el material fundido fluya hacia el molde.
Paso 5-Revestimiento de inmersión
El patrón se sumerge en una mezcla de material refractario finamente molido y luego se drena para crear un revestimiento de superficie uniforme llamado «Capa prima». Durante esta etapa, se deposita un tamaño de partícula muy fino para crear una capa delgada pero muy lisa de material de inversión, para garantizar una superficie lisa y un producto final detallado e intrincado. La sílice muy fina y otros aglutinantes, como el agua, el silicato de etilo y los ácidos, se utilizan comúnmente como materiales refractarios.
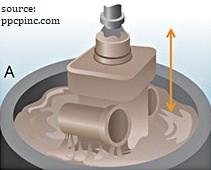
Después de que la capa inicial se haya secado, el patrón se sumerge y se recubre repetidamente para aumentar su grosor y obtener una mejor resistencia. Esta segunda etapa del proceso de inmersión se denomina «estucado», en la que se hace llover arena u otro agregado refractario sobre la superficie húmeda para aumentar el espesor (5 a 15 mm ) y la resistencia.
A veces, como método alternativo, el grupo de patrón de inmersión única se inserta en un matraz permeable boca abajo y se vierte material de inversión líquido a su alrededor. El matraz se hace vibrar para eliminar el aire atrapado y garantizar que el material de inversión rodea todas las superficies del árbol del molde.
Esto se deja secar completamente, lo que puede tardar entre 16 y 48 horas. El secado se puede acelerar aplicando un vacío o minimizando la humedad ambiental.
Paso 6-Desparafinado y cocción
Una vez que el molde de material refractario se ha secado y curado por completo, se pone boca abajo y se coloca en un horno o autoclave de desparafinado especial, donde la cera puede fundirse y agotarse (figura 7), y cualquier residuo posterior se vaporiza. (Estas simulaciones muestran cómo funcionan las máquinas depiladoras especializadas vídeo 1 o vídeo 2)

La eliminación de la cera de patrón del molde es una etapa importante en el proceso de fundición de inversión y, cuando se realiza incorrectamente, reducirá el rendimiento del lote. La depilación también es una de las principales razones del agrietamiento de la cáscara. El agrietamiento de la cáscara es el defecto de fundición de inversión más común.
Fundamentalmente hay dos métodos principales para depilación, fuego relámpago o autoclave (vapor). Los autoclaves de vapor son la opción preferida debido a su calentamiento uniforme que reduciría la tensión en el material.
El molde se calienta (90oC-175oC) y se mantiene en una posición invertida durante unas horas (aproximadamente 4-12 horas) para permitir que la cera se derrita y se agote. La cera de patrón generalmente se recupera y recicla. Luego se calienta y se mantiene a una temperatura elevada (650oC–1095oC) durante unas horas (3-6 horas), para eliminar el agua de cristalización y quemar cualquier cera residual. La duración y las temperaturas dependen del material fundido de metal.
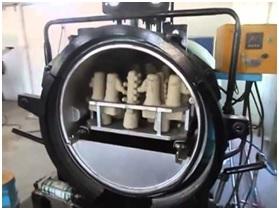
La mayoría de las fallas de la carcasa ocurren durante la etapa de desparafinado, ya que las ceras utilizadas tienen un coeficiente de expansión térmica mayor que el material refractario. Por lo tanto, la cera se expande más que el material de inversión e introduce una posible fractura por tensión en el molde. Para reducir este efecto, la cera se puede calentar rápidamente para que la cera exterior se derrita más rápido y permita que la cera restante se expanda sin estresar el molde. Los autoclaves que se muestran en la figura 8 también se utilizan para reducir este efecto, ya que los ciclos de calentamiento pueden ser más uniformes y controlarse con mayor precisión.
Paso 7-Precalentar& Fundición
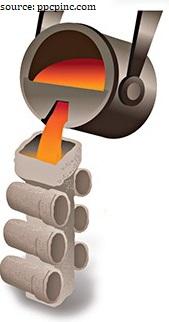
El molde se precalienta en preparación para el vertido. El precalentamiento permite que el metal permanezca en estado fundido por más tiempo para que pueda rellenar mejor todos los detalles del molde y aumentar la precisión dimensional. Si el molde se deja enfriar, las grietas encontradas se pueden reparar con lechada de cerámica o cemento especial. El calentamiento del molde también proporciona un mejor control dimensional porque el molde y el metal pueden encogerse juntos durante el enfriamiento.
Se vierte metal fundido de hasta 3000oC en el molde hueco y luego se deja enfriar. Si bien el vertido por gravedad es el más simple, se pueden usar otros métodos para garantizar el llenado completo del molde. Cuando se trata de secciones complejas y delgadas, el llenado del molde puede ser asistido por presión de aire positiva, colada basculante, colada al vacío o proceso de colada centrífuga.
Paso 8-Eliminación & postprocesamiento
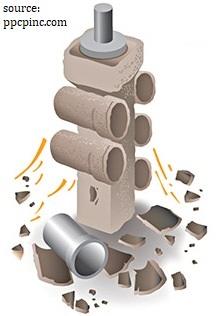
Después de que el metal se solidifica, se utilizan técnicas como astillado mecánico, martilleo, vibración, chorro de agua a alta presión y chorro de medios para romper el molde y quitar la colada de metal. A continuación, se cortan piezas fundidas individuales y se elimina el exceso de metal. El bebedero se corta y en la mayoría de los casos se reutiliza. La pieza se procesa posteriormente según los requisitos del producto final, como el post mecanizado, el tratamiento térmico, los tratamientos de superficie, la pintura, etc.
Referencias y lecturas recomendadas
- Kalpakjian, S., & Schmid, S. R. (2009). Ingeniería de fabricación & Tecnología (Sexta ed.). Londres: Pearson.
- Black, J. T, & Kohser, S. Ronald. (2012). Materials & Processing in manufacturing (Undécima ed.). Londres: John Wiley.
- Beeley, Peter, (2009). Foundry Technology (Second ed.). Oxford: Butterworth-Heinemann.
- Groover, P. Mikell, (2010). Fundamentals of modern manufacturing (Fourth ed.). Oxford: John Wiley.