Table des Matières
Étapes du processus de moulage de précision
Le moulage de précision crée des produits de forme quasi nette avec succès sous diverses formes depuis des milliers d’années. Bien que l’introduction de nouveaux matériaux et techniques de fabrication au cours des dernières années ait entraîné quelques changements et améliorations, les étapes du processus de moulage de précision sont restées en grande partie inchangées. (Vous pouvez en savoir plus sur les avantages de l’utilisation du moulage de précision ici).
En général, le moulage de précision ou parfois appelé moulage à la cire perdue peut être résumé en 8 étapes suivantes.
Étape 1 – Modèle principal
Un modèle principal est créé à partir de cire, d’argile, de bois, d’acier ou de plastique par un mouleur spécialisé ou un artiste de sculpture selon les exigences du produit final. Ceux-ci sont fabriqués en tenant compte du retrait de la cire et du matériau de coulée, d’où son nom de « modèle principal » pour avoir une tolérance de retrait double. La figure 1 ci-dessous montre un modèle de maître en bois et sa coulée.
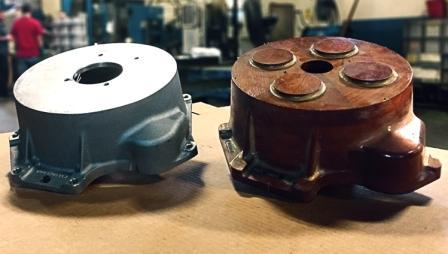
Selon la taille, la forme et le matériau utilisés, ce processus peut prendre des essais et des erreurs pour obtenir la taille et la forme correctes, ce qui rend ces moules coûteux.
Étape 2 – Matrice / moule / moule
Un moule, connu sous le nom de matrice principale pour créer des motifs de cire, est fabriqué pour s’adapter au motif principal par moulage ou usinage. Les progrès technologiques dans l’outillage et l’usinage CNC ont permis d’usiner une matrice principale à partir d’un matériau tel que l’acier et l’aluminium sans avoir besoin d’un motif principal, comme le montre la figure 2.
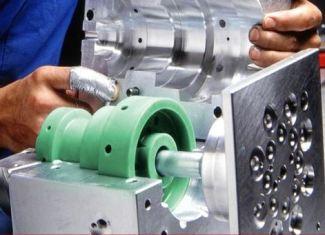
Si le modèle principal est en acier, la matrice principale peut être coulée directement à partir du modèle principal en acier en utilisant du métal avec un point de fusion inférieur à celui de l’acier. Les moules en caoutchouc de silicone sont également largement utilisés de nos jours en raison de leur simplicité d’utilisation pour mouler un moule directement à partir d’un modèle principal. Les moules en caoutchouc de silicone résisteraient à une température de coulée allant jusqu’à environ 310oC (590oF).
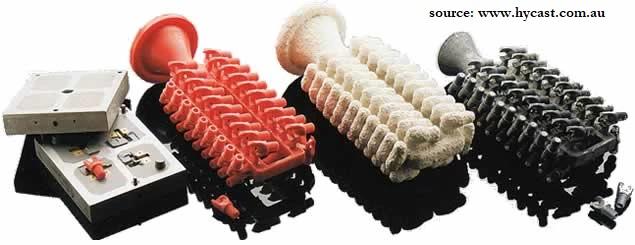
Le modèle principal et la matrice principale doivent être conçus en tenant compte du retrait de la cire à motifs, du matériau réfractaire et du matériau moulé en métal. Il est également recommandé d’ajouter des tolérances d’usinage pour le post-usinage sur des surfaces à tolérance plus serrée. Un autre aspect important des matrices maîtresses ou des moules en deux parties est les localisateurs d’alignement des moules. Les localisateurs de moules sont essentiels pour aligner les deux moitiés afin de produire des pièces précises sans grandes lignes de séparation ni décalages de ligne de séparation. (Figure 3)
Étape 3 – Motif
Les motifs sont ensuite réalisés en injectant ou en versant de la cire fondue dans la matrice principale et en la laissant durcir (Figure 4). Parfois, il est également utilisé comme revêtement où les parois intérieures de la cavité de la matrice sont recouvertes de cire pour obtenir un motif creux. Ce revêtement est répété jusqu’à ce que l’épaisseur de motif souhaitée soit généralement d’environ 3 mm (0,12 po). Ce dernier ne convient que pour des pièces simples. Parfois, des motifs sont également fabriqués à l’aide de polymères appropriés et de mercure congelé.
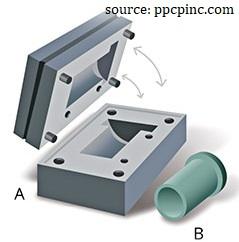
Les progrès récents du prototypage rapide ont rendu possible la production de motifs directement à partir d’un fichier CAO, soit en tant que motif principal, soit en tant que motif en cire, réduisant ainsi le coût. Les technologies d’impression 3D telles que la stéréolithographie, le frittage laser sélectif (SLS), la modélisation par dépôt fondu (FDM) et le poly jet sont de plus en plus utilisées pour créer des motifs. Ces technologies de prototypage rapide utilisent une technique de superposition dans leur création, de sorte qu’un post-traitement est nécessaire dans la plupart des cas pour assurer une bonne finition de surface.
Les noyaux sont généralement fabriqués à partir de cire soluble ou de céramique où des noyaux de cire solubles sont dissous hors des motifs prétraitement, tandis que les noyaux en céramique restent et sont éliminés après solidification de la coulée de métal.
Dans un processus appelé « Chasse », les imperfections telles que les lignes de séparation et les solins sont éliminées à l’aide d’un outil métallique chauffé et des agents de démoulage, tels que des sprays en silicone, sont également utilisés pour faciliter l’enlèvement des motifs et éviter tout dommage aux motifs.
Étape 4 – Assemblage des motifs
Les motifs de cire sont ensuite assemblés sur une coulée de cire commune. La sprue est un canal à travers lequel l’alliage fondu peut atteindre le moule dans un anneau d’investissement après l’élimination de la cire.
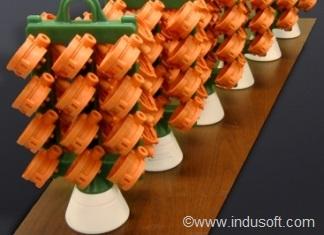
À l’aide d’outils chauffants et de cire fondue, un certain nombre de motifs de cire peuvent être fixés à un système central de sprue et de coureur pour créer un cluster de motifs ou un arbre. Selon la taille des pièces, jusqu’à plusieurs centaines de motifs peuvent être assemblés sur un arbre augmentant la productivité. (Figure 5)
Sprue retiendra le motif de cire pour éviter toute distorsion pendant le processus de coulée, créant un canal pour que la cire fondue s’échappe du moule, puis permettant au matériau fondu de s’écouler dans le moule.
Étape 5 – Revêtement de trempage
Le motif est ensuite plongé dans une suspension de matériau réfractaire finement broyé, puis égoutté pour créer un revêtement de surface uniforme appelé « couche de base ». Au cours de cette étape, une granulométrie très fine est déposée pour créer une couche mince mais très lisse de matériau d’investissement, afin d’assurer une surface lisse et un produit final détaillé et complexe. La silice très fine et d’autres liants, y compris l’eau, le silicate d’éthyle et les acides, sont couramment utilisés comme matériaux réfractaires.
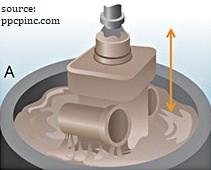
Après séchage de la couche initiale, le motif est trempé et enduit à plusieurs reprises pour augmenter son épaisseur pour une meilleure résistance. Cette deuxième étape du processus de trempage est appelée « stucage » dans lequel on fait pleuvoir du sable ou autre agrégat réfractaire sur la surface humide pour augmenter l’épaisseur (5 à 15 mm) et la résistance.
Parfois, comme méthode alternative, le groupe de motifs à un seul plongement est inséré dans un flacon perméable à l’envers et du matériau d’investissement liquide est versé autour de celui-ci. Le flacon est ensuite mis en vibration pour éliminer l’air emprisonné et s’assurer que le matériau d’investissement entoure toutes les surfaces de l’arbre à moules.
On laisse ensuite sécher complètement, ce qui peut prendre entre 16 et 48 heures. Le séchage peut être accéléré en appliquant un vide ou en minimisant l’humidité ambiante.
Étape 6 – Dé-cirage et cuisson
Une fois que le moule de matériau réfractaire a complètement séché et durci, ils sont retournés et placés dans un four ou un autoclave de dé-cirage à usage spécial, où la cire peut fondre et s’épuiser (figure 7), et tout résidu ultérieur vaporisé. (Ces simulations montrent comment fonctionnent les machines de dépilage spécialisées vidéo 1 ou vidéo 2)

L’élimination de la cire à modeler du moule est une étape importante du processus de moulage de précision et, lorsqu’elle est mal exécutée, elle réduit le rendement du lot. L’épilation à la cire est également l’une des principales raisons de la fissuration de la coquille. La fissuration de la coque est le défaut de coulée d’investissement le plus courant.
Fondamentalement, il existe deux méthodes principales pour le démâtage, le feu éclair ou l’autoclave (vapeur). Les autoclaves à vapeur sont le choix préféré en raison de leur chauffage uniforme qui réduirait les contraintes sur le matériau.
Le moule est chauffé (90oC-175oC) et maintenu en position inversée pendant quelques heures (environ 4 à 12 heures) pour permettre à la cire de fondre et de s’épuiser. La cire à motifs est généralement récupérée et recyclée. Ensuite, il est chauffé et maintenu à une température élevée (650oC-1095oC) pendant quelques heures (3-6 heures), pour chasser l’eau de cristallisation et brûler toute cire résiduelle. La durée et les températures dépendent du matériau moulé en métal.
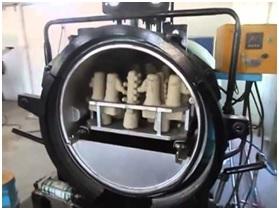
La plupart des défaillances de la coque se produisent pendant l’étape de déparaffinage car les cires utilisées ont un coefficient de dilatation thermique plus élevé que le matériau réfractaire. Par conséquent, la cire se dilate plus que le matériau d’investissement et introduit une éventuelle fracture de contrainte sur le moule. Pour réduire cet effet, la cire peut être chauffée rapidement afin que la cire extérieure fond plus rapidement et permette à la cire restante de se dilater sans forcer le moule. Les autoclaves illustrés à la figure 8 sont également utilisés pour réduire cet effet car les cycles de chauffage peuvent être plus uniformes et contrôlés avec plus de précision.
Étape 7 – Préchauffage & Coulée
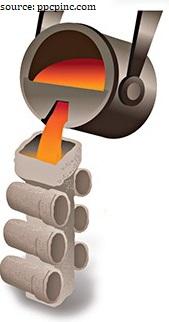
Le moule est ensuite préchauffé en préparation du coulage. Le préchauffage permet au métal de rester plus longtemps à l’état fondu afin de mieux remplir tous les détails du moule et d’augmenter la précision dimensionnelle. Si le moule est laissé refroidir, les fissures trouvées peuvent être réparées avec de la boue céramique ou du ciment spécial. Le chauffage du moule permet également un meilleur contrôle dimensionnel car le moule et le métal peuvent rétrécir ensemble pendant le refroidissement.
Du métal en fusion jusqu’à 3000oC est versé dans le moule creux puis laissé refroidir. Bien que le coulage par gravité soit le plus simple, d’autres méthodes peuvent être utilisées pour assurer un remplissage complet du moule. Lorsque des sections complexes et minces sont impliquées, le remplissage du moule peut être assisté par une pression d’air positive, une coulée par inclinaison, une coulée sous vide ou un processus de coulée par centrifugation.
Étape 8 – Knockout & post-traitement
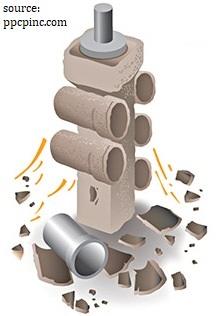
Une fois le métal solidifié, des techniques telles que l’écaillage mécanique, le martelage, la vibration, le jet d’eau à haute pression et le dynamitage sont utilisées pour briser le moule et retirer la coulée de métal. Ensuite, les pièces moulées individuelles sont coupées et l’excès de métal est enlevé. La carotte est coupée et dans la plupart des cas réutilisée. La pièce est ensuite post-traitée selon les exigences du produit final telles que le post-usinage, le traitement thermique, les traitements de surface, la peinture, etc.
Références et lectures recommandées
- Kalpakjian, S., & Schmid, S.R. (2009). Ingénierie de fabrication & Technologie (Sixième éd.). Londres : Pearson.
- Noir, J. T, & Kohser, S. Ronald. (2012). Matériaux & Transformation en fabrication (Onzième éd.). Londres : John Wiley.
- Beeley, Peter, (2009). Technologie de fonderie (Deuxième éd.). Il s’agit d’un personnage de fiction.
- Groover, P. Mikell, (2010). Principes fondamentaux de la fabrication moderne (quatrième éd.). Il y a des gens qui sont là.