Indice
Fasi del processo di microfusione
La microfusione ha creato con successo prodotti a forma quasi netta in varie forme per migliaia di anni. Sebbene l’introduzione di nuovi materiali e tecniche di produzione negli ultimi anni abbia portato ad alcuni cambiamenti e miglioramenti, le fasi del processo di microfusione sono rimaste in gran parte invariate. (Puoi leggere i vantaggi dell’utilizzo della microfusione qui).
In generale, la microfusione o talvolta indicata come fusione a cera persa può essere riassunta nei seguenti 8 passaggi.
Fase 1 – Modello master
Un modello master viene creato da cera, argilla, legno, acciaio o plastica da uno stampo specializzato o artista scultura secondo il requisito del prodotto finale. Questi sono fatti considerando sia la cera che il restringimento del materiale di fusione, quindi è chiamato “modello principale” per avere una doppia tolleranza di restringimento. La figura 1 sotto mostra un modello master in legno e la sua fusione.
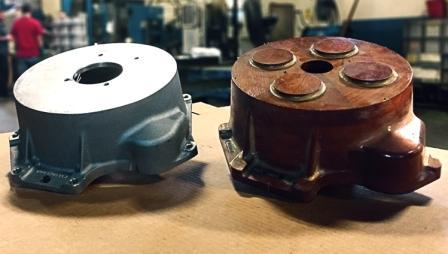
A seconda delle dimensioni, della forma e del materiale utilizzato, questo processo può richiedere alcuni tentativi ed errori per ottenere la dimensione e la forma corrette, rendendo quindi costosi questi stampi.
Fase 2-Master die / Mould / Mold
Uno stampo, noto come master die per creare modelli di cera, è realizzato per adattarsi al modello master mediante fusione o lavorazione. Il progresso tecnologico nella lavorazione con utensili e nella lavorazione CNC ha permesso di lavorare uno stampo master da un materiale come l’acciaio e l’alluminio senza la necessità di un modello master come mostrato in figura 2.
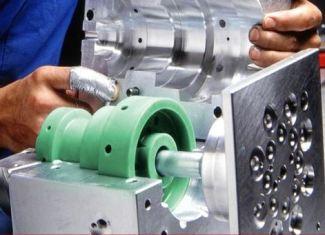
Se il modello master è realizzato in acciaio, il master die può essere fuso direttamente dal modello master in acciaio utilizzando metallo con un punto di fusione inferiore rispetto all’acciaio. Gli stampi in gomma siliconica sono ampiamente utilizzati in questi giorni grazie alla loro semplicità di utilizzo per lanciare uno stampo direttamente da un modello master. Gli stampi in gomma siliconica resisterebbero a temperature di fusione fino a circa 310oC (590oF).
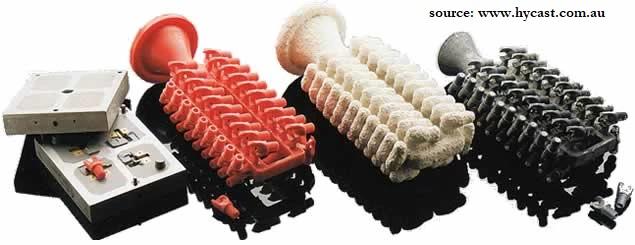
Il modello master e il master die devono essere progettati tenendo conto del restringimento della cera del modello, del materiale refrattario e del materiale fuso metallico. È anche buona pratica aggiungere quote di lavorazione per la post-lavorazione su superfici di tolleranza più strette. Un altro aspetto importante delle matrici o degli stampi master in due parti sono i localizzatori di allineamento degli stampi. I localizzatori di stampi sono fondamentali per allineare le due metà per produrre parti accurate senza grandi linee di separazione o spostamenti di linee di separazione. (Figura 3)
Fase 3 – Modello
I modelli vengono quindi realizzati iniettando o versando cera fusa nello stampo master e permettendone l’indurimento (Figura 4). A volte è anche usato come rivestimento in cui le pareti interne della cavità dello stampo sono rivestite con cera per ottenere un motivo cavo. Questo rivestimento viene ripetuto fino a raggiungere lo spessore del motivo desiderato di solito circa 3 mm (0,12 pollici). Quest’ultimo adatto solo per parti semplici. A volte i modelli sono realizzati anche utilizzando polimeri adatti e mercurio congelato.
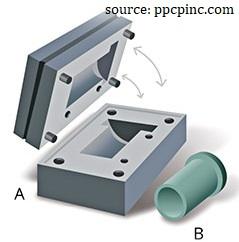
I recenti progressi nella prototipazione rapida hanno reso possibile la produzione di modelli direttamente da un file CAD, sia come modello master che come modelli in cera, riducendo di conseguenza i costi. Le tecnologie di stampa 3D come la stereolitografia, la sinterizzazione laser selettiva (SLS), la modellazione a deposizione fusa (FDM) e il poli getto sono sempre più utilizzate per creare modelli. Queste tecnologie di prototipazione rapida utilizzano una tecnica di stratificazione nella loro creazione, quindi nella maggior parte dei casi è necessaria la post-elaborazione per garantire una buona finitura superficiale.
I nuclei sono generalmente realizzati in cera solubile o ceramica dove i nuclei di cera solubili vengono sciolti dai modelli di pre-elaborazione, mentre i nuclei ceramici rimangono e vengono rimossi dopo la solidificazione della fusione metallica.
In un processo chiamato “Inseguire” le imperfezioni come le linee di separazione e le infiammazioni vengono rimosse utilizzando uno strumento metallico riscaldato e gli agenti di rilascio, come gli spray al silicone, vengono utilizzati anche per aiutare nella rimozione del motivo ed evitare qualsiasi danno ai motivi.
Fase 4 – Assemblaggio del modello
I modelli di cera vengono quindi assemblati su una comune colata di cera. Sprue è un canale attraverso il quale la lega fusa può raggiungere lo stampo in un anello di investimento dopo che la cera è stata eliminata.
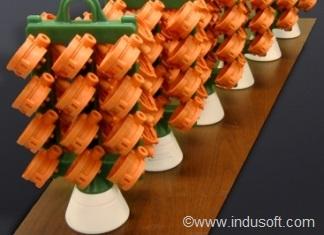
Utilizzando strumenti riscaldati e cera fusa, è possibile collegare una serie di modelli di cera a un sistema centrale di materozza e canale per creare un cluster di pattern o un albero. A seconda delle dimensioni delle parti, fino a diverse centinaia di modelli possono essere assemblati su un albero aumentando la produttività. (Figura 5)
La sprue manterrà il modello di cera per evitare distorsioni durante il processo di fusione, creando un canale per la fuoriuscita della cera fusa dallo stampo e quindi consentendo al materiale fuso di fluire nello stampo.
Fase 5 – Rivestimento per immersione
Il modello viene quindi immerso in un impasto di materiale refrattario finemente macinato e quindi drenato per creare un rivestimento superficiale uniforme chiamato “rivestimento primario”. Durante questa fase viene depositata una granulometria molto fine per creare uno strato sottile ma molto liscio di materiale di investimento, per garantire una superficie liscia e un prodotto finale complesso e dettagliato. Silice molto fine e altri leganti, tra cui acqua, silicato di etile e acidi sono comunemente usati come materiali refrattari.
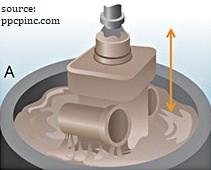
Dopo che lo strato iniziale si è asciugato, il motivo viene immerso e rivestito ripetutamente per aumentare lo spessore per una migliore resistenza. Questa seconda fase del processo di immersione è chiamata “stuccatura” in cui sabbia o altro aggregato refrattario viene piovuto sulla superficie bagnata per aumentare lo spessore (da 5 a 15 mm ) e la resistenza.
A volte come metodo alternativo, il cluster di pattern a immersione singola viene inserito in un pallone permeabile capovolto e il materiale di investimento liquido viene versato attorno ad esso. Il pallone viene quindi vibrato per rimuovere l’aria intrappolata e garantire che il materiale di investimento circonda tutte le superfici dell’albero dello stampo.
Questo viene quindi lasciato asciugare completamente, il che può richiedere da 16 a 48 ore. L’essiccazione può essere accelerata applicando un vuoto o riducendo al minimo l’umidità ambientale.
Fase 6 – Deceratura e cottura
Una volta che lo stampo del materiale refrattario è completamente essiccato e stagionato, questi vengono capovolti e posti in un forno o in un’autoclave speciale di deceratura, dove la cera può fondersi e esaurirsi (figura 7), e ogni residuo successivo vaporizzato. (Queste simulazioni mostrano come funzionano le macchine di deceratura specializzate video 1 o video 2)

La rimozione della cera da stampo è una fase importante nel processo di microfusione e, se eseguita in modo errato, riduce la resa del lotto. La deceratura è anche uno dei motivi principali per il cracking del guscio. Il cracking delle coperture è il singolo difetto di fusione di investimento più comune.
Fondamentalmente ci sono due metodi principali per la deceratura, il fuoco istantaneo o l’autoclave (vapore). Le autoclavi a vapore sono la scelta preferita a causa del loro riscaldamento uniforme che ridurrebbe lo stress sul materiale.
Lo stampo viene riscaldato (90oC–175oC) e tenuto in posizione invertita per alcune ore (circa 4 – 12 ore) per consentire alla cera di sciogliersi e esaurirsi. La cera del modello è recuperata solitamente e riciclata. Quindi viene riscaldato e mantenuto ad una temperatura elevata (650oC–1095oC) per alcune ore (3-6 ore), per allontanare l’acqua di cristallizzazione e bruciare qualsiasi cera residua. La durata e le temperature dipendono dal materiale fuso metallico.
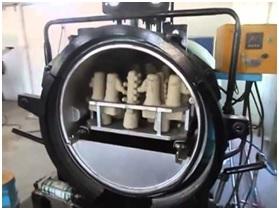
La maggior parte dei guasti del guscio si verificano durante la fase di deparaffinazione poiché le cere utilizzate hanno un coefficiente di dilatazione termica maggiore rispetto al materiale refrattario. Quindi la cera si espande più del materiale di investimento e introduce una possibile frattura da stress sullo stampo. Per ridurre questo effetto la cera può essere riscaldata rapidamente in modo che la cera esterna si sciolga più velocemente e permetta alla cera rimanente di espandersi senza stressare lo stampo. Le autoclavi mostrate in figura 8 sono anche utilizzate per ridurre questo effetto di calore poiché i cicli di riscaldamento possono essere più uniformi e controllati in modo più accurato.
Fase 7-Preriscaldamento & Fusione
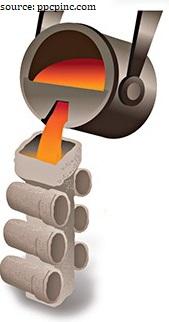
Lo stampo viene quindi preriscaldato in preparazione al versamento. Il preriscaldamento consente al metallo di rimanere più a lungo allo stato fuso in modo da poter riempire meglio tutti i dettagli dello stampo e aumentare la precisione dimensionale. Se lo stampo viene lasciato raffreddare, eventuali crepe riscontrate possono essere riparate con liquami ceramici o cemento speciale. Il riscaldamento della muffa inoltre dà il migliore controllo dimensionale perché la muffa ed il metallo possono restringersi insieme durante il raffreddamento.
Il metallo fuso fino a 3000oC viene versato nello stampo cavo e poi lasciato raffreddare. Mentre gravità versando è il più semplice, altri metodi possono essere utilizzati per garantire il riempimento completo dello stampo. Quando sono coinvolte sezioni complesse e sottili, il riempimento dello stampo può essere assistito da pressione d’aria positiva, colata inclinata, colata sotto vuoto o processo di colata centrifuga.
Fase 8-Knockout & post-elaborazione
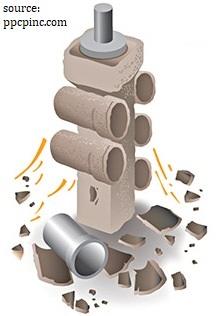
Dopo che il metallo si è solidificato, vengono utilizzate tecniche come la scheggiatura meccanica, il martellamento, la vibrazione, il getto d’acqua ad alta pressione e la sabbiatura dei media per rompere lo stampo e rimuovere la fusione metallica. Quindi i singoli getti vengono tagliati e il metallo in eccesso viene rimosso. La sprue viene tagliata e nella maggior parte dei casi riutilizzata. La parte viene quindi post-elaborata secondo il requisito del prodotto finale come post-lavorazione, trattamento termico, trattamenti superficiali,verniciatura ecc.
Riferimenti e letture consigliate
- Kalpakjian, S., & Schmid, SR (2009). Ingegneria di produzione & Tecnologia (Sesta ed.). Londra: Pearson.
- Nero, J. T, & Kohser, S. Ronald. (2012). Materiali & Lavorazione nella produzione (Undicesima ed.). Londra: John Wiley.
- Beeley, Peter, (2009). Tecnologia di fonderia (Seconda ed.). Oxford: Butterworth-Heinemann.
- Groover, P. Mikell, (2010). Fondamenti della produzione moderna (Quarta ed.). John Wiley.