inhoudsopgave:
investeringen gieten proces stappen
investeringen gieten is het creëren van near-net shape producten met succes in verschillende vormen voor duizenden jaren. Hoewel de invoering van nieuwe materialen en fabricagetechnieken in de afgelopen jaren tot enkele veranderingen en verbeteringen heeft geleid, zijn de stappen van het investeringsgietproces grotendeels ongewijzigd gebleven. (U kunt lezen over de voordelen van het gebruik van investment casting hier).
in het algemeen kunnen investeringsgieten of soms verloren-wasgieten genoemd, in de volgende 8 stappen worden samengevat.
Stap 1-hoofdpatroon
een hoofdpatroon wordt gemaakt van was, klei, hout, staal of kunststof door een gespecialiseerde vormmaker of beeldhouwkunstenaar volgens de eis van het eindproduct. Deze zijn gemaakt rekening houdend met zowel wax en gieten materiaal krimp, vandaar dat het heet, “master patroon” voor het hebben van dubbele krimp vergoeding. Figuur 1 hieronder toont een houten hoofdpatroon en het gieten ervan.
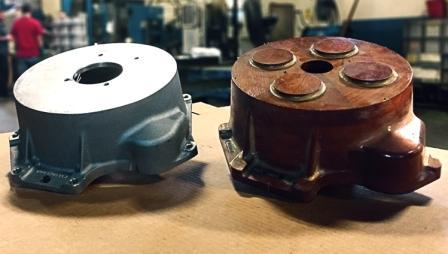
afhankelijk van de grootte, vorm en materiaal gebruikt, kan dit proces enige trial and error nemen om de grootte en vorm correct te krijgen, waardoor deze mallen duur zijn.
Stap 2-Master matrijs / mal / mal
een mal, bekend als de master matrijs om waspatronen te maken, wordt gemaakt om in het masterpatroon te passen door te gieten of te bewerken. De technologische vooruitgang op het gebied van tooling en CNC-bewerking heeft het mogelijk gemaakt om een mastermatrijs van een materiaal zoals staal en aluminium te bewerken zonder dat er een masterpatroon nodig is, zoals weergegeven in Figuur 2.
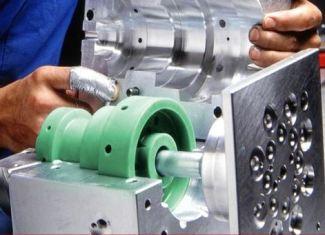
als het masterpatroon van staal is gemaakt, kan de mastermatrijs rechtstreeks uit het stalen masterpatroon worden gegoten met metaal met een lager smeltpunt dan staal. Siliconen rubber mallen worden ook veel gebruikt deze dagen vanwege hun eenvoud van het gebruik om een mal direct uit een master patroon gegoten. Siliconenrubber mallen zouden bestand zijn tegen casting temperatuur tot ongeveer 310oC (590oF).
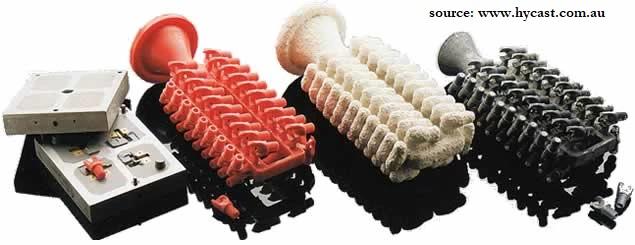
Stap 3 – Patroon
de patronen worden vervolgens gemaakt door het injecteren of gieten van gesmolten was in de matrijs en het laten uitharden (Figuur 4). Soms wordt het ook gebruikt als een coating waar binnen spouwwanden van de matrijs zijn bekleed met was om een hol patroon te krijgen. Deze coating wordt herhaald tot de gewenste patroondikte meestal ongeveer 3 mm (0,12 in) is bereikt. Laatste alleen geschikt voor eenvoudige onderdelen. Soms worden patronen ook gemaakt met behulp van geschikte polymeren en bevroren kwik.
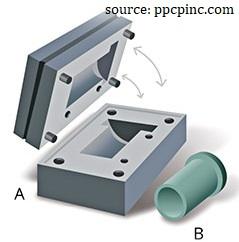
recente ontwikkelingen op het gebied van rapid prototyping hebben de productie van patronen rechtstreeks uit een CAD-bestand mogelijk gemaakt, hetzij als basispatroon, hetzij als waspatronen, waardoor de kosten werden verlaagd. 3D-printtechnologieën zoals stereolithografie, selective laser sintering (SLS), fused deposition modelling (FDM) en poly jetting worden steeds vaker gebruikt om patronen te creëren. Deze snelle prototyping technologieën gebruiken een gelaagdheid techniek in hun creatie zodat post-processing is vereist in de meeste gevallen om een goede oppervlakte-afwerking te garanderen.
kernen zijn over het algemeen gemaakt van oplosbare was of keramiek waarbij oplosbare waskernen worden opgelost uit de voorbewerking van de patronen, terwijl de keramische kernen blijven en worden verwijderd na stolling van het metaalgietwerk.
in een proces dat “het najagen” wordt genoemd, worden onvolkomenheden zoals scheidingslijnen en knipperingen verwijderd met een verwarmd metaalgereedschap en worden ontgrendelingsmiddelen, zoals siliconensprays, ook gebruikt om patroonverwijdering te helpen en schade aan de patronen te voorkomen.
Stap 4-Patroonassemblage
de waspatronen worden vervolgens geassembleerd op een gewone waxsprue. Sprue is een kanaal waardoor gesmolten legering de mal in een investeringsring kan bereiken nadat de was is geëlimineerd.
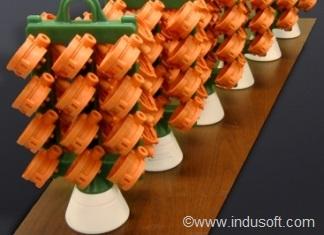
met verwarmd gereedschap en gesmolten was kan een aantal waspatronen worden bevestigd aan een centrale sprue en runner-systeem om een patrooncluster of een boom te creëren. Afhankelijk van de grootte van de onderdelen, kunnen tot enkele honderden patronen worden gemonteerd op een boom verhogen van de productiviteit. (Figuur 5)
Sprue houdt het waspatroon vast om vervorming tijdens het gietproces te voorkomen, waardoor een kanaal wordt gecreëerd waardoor de gesmolten was uit de mal kan ontsnappen en het gesmolten materiaal vervolgens in de mal kan stromen.
Stap 5-Dompelcoating
het patroon wordt vervolgens ondergedompeld in een mengmest van fijngemalen vuurvast materiaal en vervolgens afgevoerd tot een uniforme oppervlaktelaag, een “Prime coat”genoemd. Tijdens deze fase wordt een zeer fijne deeltjesgrootte afgezet om een dunne maar zeer gladde laag investeringsmateriaal te creëren, om een glad oppervlak en ingewikkelde gedetailleerde eindproduct te garanderen. Zeer fijn silica en andere bindmiddelen, waaronder water, ethylsilicaat en zuren worden vaak gebruikt als vuurvaste materialen.
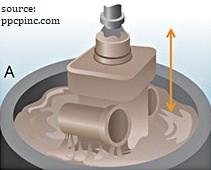
nadat de initiële laag is opgedroogd, wordt het patroon herhaaldelijk ondergedompeld en gecoat om de dikte te vergroten voor een betere sterkte. Deze tweede fase van het dompelproces wordt “stucwerk” genoemd, waarbij zand of ander vuurvast aggregaat over het natte oppervlak wordt geregend om de dikte (5 tot 15 mm ) en de sterkte te verhogen.
bij wijze van Alternatief wordt de cluster met enkelvoudig gedimde patronen ondersteboven in een permeabele kolf geplaatst en eromheen vloeibaar investeringsmateriaal gegoten. De kolf wordt vervolgens getrild om ingesloten lucht te verwijderen en ervoor te zorgen dat het investeringsmateriaal alle oppervlakken van de matrijzenboom omringt.
dit wordt dan volledig droog gelaten, wat 16 tot 48 uur kan duren. Het drogen kan worden versneld door het aanbrengen van een vacuüm of het minimaliseren van de omgevingsvochtigheid.
Stap 6-ontwassen en bakken
zodra de vorm van het vuurvaste materiaal volledig is gedroogd en uitgehard, worden ze ondersteboven gekeerd en in een oven of een speciale ontwassende autoclaaf geplaatst, waar de was kan smelten en opraken (figuur 7), en eventuele restanten worden verdampt. (Deze simulaties laten zien hoe gespecialiseerde ontharingsmachines werken video 1 of video 2)

het verwijderen van patroonwas uit de mal is een belangrijke fase in het investeringsgietproces en zal, indien onjuist uitgevoerd, het batchrendement verminderen. De-waxen is ook een van de belangrijkste redenen voor shell kraken. Shell kraken is de meest voorkomende investeren gieten defect.
fundamenteel zijn er twee hoofdmethoden voor het ontwassen, flitsbrand of autoclaaf (stoom). Stoomautoclaven zijn de voorkeur vanwege hun uniforme verwarming die de stress op het materiaal zou verminderen.
de vorm wordt verwarmd (90oC-175oC) en gedurende een paar uur (ongeveer 4-12 uur) omgekeerd gehouden om de was te laten smelten en op te laten lopen. Patroonwas wordt meestal teruggewonnen en gerecycled. Dan wordt het verwarmd en bij een opgeheven temperatuur (650oC–1095oC) voor een paar uren (3-6 uren) gehandhaafd, om van het water van kristallisatie te drijven en om het even welke overblijvende was af te branden. De duur en de temperaturen zijn afhankelijk van het metaalgietmateriaal.
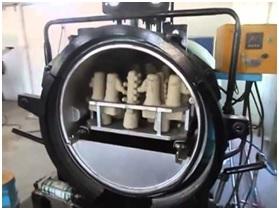
de meeste defecten in de schaal treden op tijdens de wasfase, omdat de gebruikte was een grotere thermische uitzettingscoëfficiënt heeft dan het vuurvaste materiaal. Wax breidt dus meer uit dan het investeringsmateriaal en introduceert een mogelijke spanningsbreuk op de matrijs. Om dit effect te verminderen kan de was snel worden verhit zodat de buitenwas sneller smelt en de resterende was kan uitzetten zonder de mal te belasten. De in figuur 8 getoonde autoclaven worden ook gebruikt om dit effect te verminderen aangezien de verwarmingscycli meer uniform en nauwkeuriger kunnen worden gecontroleerd.
Stap 7-verwarm& gieten
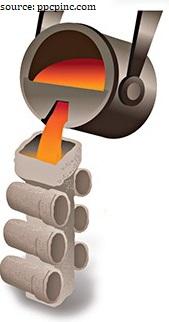
de mal wordt vervolgens voorverwarmd ter voorbereiding op het gieten. Door voorverwarming kan het metaal langer in de gesmolten toestand blijven, zodat het alle matrijsdetails beter kan vullen en de maatnauwkeurigheid kan verhogen. Als de mal wordt gelaten om te koelen, eventuele scheuren kunnen worden gerepareerd met keramische drijfmest of speciaal cement. Matrijsverwarming geeft ook een betere maatregeling omdat de matrijs en het metaal tijdens het koelen samen kunnen krimpen.
gesmolten metaal tot 3000oC wordt in de holle mal gegoten en vervolgens afgekoeld. Terwijl de zwaartekracht gieten is de eenvoudigste, andere methoden kunnen worden gebruikt om volledige vulling van de mal te garanderen. Wanneer het gaat om complexe, dunne secties, kan het vullen van matrijzen worden ondersteund door positieve luchtdruk, kantelgieten, vacuümgieten of centrifugaalgietproces.
Stap 8-Knockout & nabewerking
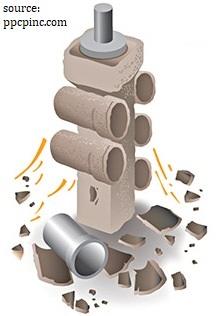
nadat het metaal is gestold, worden technieken zoals Mechanisch chippen, hameren, trillen, waterstralen onder hoge druk en mediastralen gebruikt om de mal te breken en het metaalgieten te verwijderen. Vervolgens worden individuele gietstukken weggesneden en overtollig metaal verwijderd. De sprue wordt afgesneden en in de meeste gevallen hergebruikt. Het deel wordt dan post-verwerkt volgens de uiteindelijke productvereiste zoals post-machinaal bewerken, warmtebehandeling, oppervlaktebehandelingen, schilderen enz.
referenties en aanbevolen lezing
- Kalpakjian, S., & Schmid, S. R. (2009). Productietechniek & technologie (zesde uitgave.). London: Pearson.
- Black, J. T, & Kohser, S. Ronald. (2012). Materialen & verwerking in de verwerkende industrie (elfde ed.). London: John Wiley.
- Beeley, Peter, (2009). Gieterij technologie (tweede ed.). Oxford: Butterworth-Heinemann.
- Groover, P. Mikell, (2010). Fundamentals of modern manufacturing (Fourth ed.). Oxford: John Wiley.