spis treści
etapy procesu odlewania inwestycyjnego
Odlewanie inwestycyjne od tysięcy lat tworzy produkty o kształcie zbliżonym do netto w różnych formach. Chociaż wprowadzenie nowych materiałów i technik wytwarzania w ciągu ostatnich kilku lat doprowadziło do pewnych zmian i ulepszeń, etapy procesu odlewania inwestycyjnego w dużej mierze pozostały niezmienione. (O zaletach stosowania odlewów inwestycyjnych można przeczytać tutaj).
ogólnie rzecz biorąc, odlewanie inwestycyjne lub czasami określane jako odlewanie wosku traconego można podsumować w następujących 8 krokach.
Krok 1 – Wzór główny
wzór główny jest tworzony z wosku, gliny, drewna, stali lub plastiku przez wyspecjalizowanego producenta form lub rzeźbiarza zgodnie z wymaganiami produktu końcowego. Są one wykonane biorąc pod uwagę zarówno kurczenie się wosku, jak i materiału odlewniczego, stąd nazywa się to „wzorcem wzorcowym”, aby uzyskać podwójny naddatek skurczu. Rysunek 1 poniżej przedstawia drewniany wzór główny i jego odlewanie.
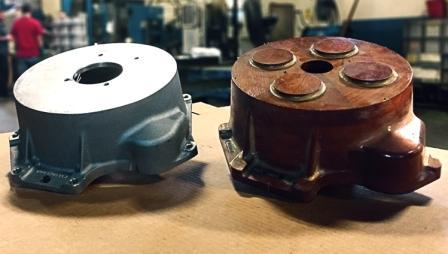
w zależności od rozmiaru, kształtu i użytego materiału proces ten może wymagać pewnych prób i błędów, aby uzyskać prawidłowy rozmiar i kształt, dlatego te formy są drogie.
Krok 2-Master die / Mould / Mold
forma, znana jako master die do tworzenia wzorów woskowych, jest dopasowana do wzorca głównego poprzez odlewanie lub obróbkę. Postęp technologiczny w oprzyrządowaniu i obróbce CNC umożliwił obróbkę matrycy wzorcowej z materiału takiego jak stal i aluminium bez potrzeby stosowania wzorca wzorcowego, jak pokazano na rysunku 2.
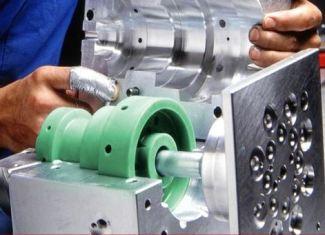
jeśli wzór główny jest wykonany ze stali, matryca główna może być odlewana bezpośrednio ze wzoru stalowego przy użyciu metalu o niższej temperaturze topnienia niż stal. Formy z gumy silikonowej są obecnie szeroko stosowane ze względu na ich prostotę użycia do odlewania formy bezpośrednio z wzoru głównego. Formy z gumy silikonowej wytrzymałyby temperaturę odlewania do około 310oC (590oF).
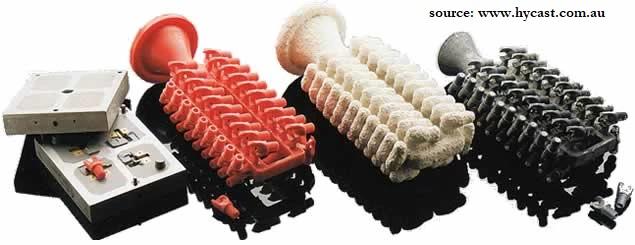
wzór główny i matryca główna muszą być zaprojektowane z uwzględnieniem skurczu wosku wzorcowego, materiału ogniotrwałego i odlewanego metalu. Dobrą praktyką jest również dodawanie uprawnień obróbkowych do obróbki końcowej na bardziej ciasnych powierzchniach tolerancji. Innym ważnym aspektem dwuczęściowych matryc lub form głównych są lokalizatory wyrównania formy. Lokalizatory form mają kluczowe znaczenie w wyrównywaniu dwóch połówek w celu uzyskania dokładnych części bez dużych linii podziału lub przesunięć linii podziału. (Rysunek 3)
Krok 3-Wzór
wzory są następnie wykonywane przez wstrzyknięcie lub wlanie stopionego wosku do matrycy głównej i umożliwienie jej stwardnienia (Rysunek 4). Czasami jest również stosowany jako powłoka, w której wewnętrzne ściany wnęki matrycy są pokryte woskiem, aby uzyskać pusty wzór. Powłokę tę powtarza się, aż pożądana grubość wzoru osiągnie zwykle około 3 mm (0,12 cala). Ten ostatni nadaje się tylko do prostych części. Czasami wzory są również wykonane przy użyciu odpowiednich polimerów i zamrożonej rtęci.
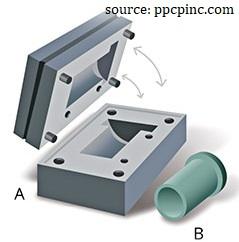
ostatnie postępy w szybkim prototypowaniu umożliwiły produkcję wzorów bezpośrednio z pliku CAD, zarówno jako wzór główny, jak i wzory woskowe, co obniżyło koszty. Technologie druku 3D, takie jak Stereolitografia, selektywne spiekanie laserowe (SLS), modelowanie osadzania stapianego (FDM) i poly jetting są coraz częściej wykorzystywane do tworzenia wzorów. Te technologie szybkiego prototypowania wykorzystują technikę warstwową w ich tworzeniu, więc w większości przypadków wymagane jest przetwarzanie końcowe, aby zapewnić dobre wykończenie powierzchni.
rdzenie są zwykle wykonane z rozpuszczalnego wosku lub ceramiki, w których rozpuszczalne rdzenie woskowe są rozpuszczane z wzorów obróbki wstępnej, podczas gdy rdzenie ceramiczne pozostają i są usuwane po zestaleniu odlewu metalowego.
w procesie zwanym „ściganiem” niedoskonałości, takich jak linie podziału i obróbka, są usuwane za pomocą podgrzewanego narzędzia metalowego, a środki antyadhezyjne, takie jak silikonowe spraye, są również używane do usuwania wzorów i unikania uszkodzeń wzorów.
Krok 4 – Montaż wzoru
wzory wosku są następnie montowane na wspólnej wlew wosku. Wlew jest kanałem, przez który stopiony stop może dotrzeć do formy w pierścieniu po usunięciu wosku.
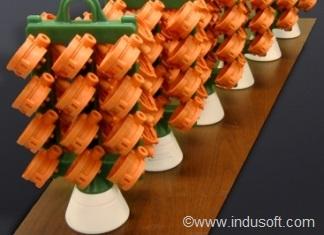
za pomocą podgrzewanych narzędzi i stopionego wosku można przymocować wiele wzorów wosku do centralnego systemu wlewu i prowadnic, aby utworzyć klaster wzorów lub drzewo. W zależności od wielkości części, na drzewie można zmontować do kilkuset wzorów zwiększając produktywność. (Rysunek 5)
wlew utrzyma wzór wosku, aby uniknąć zniekształceń podczas procesu odlewania, tworząc kanał dla stopionego wosku, aby wydostać się z formy, a następnie umożliwiając płynny materiał do formy.
Krok 5-powłoka zanurzeniowa
wzór jest następnie zanurzany w zawiesinie drobno zmielonego materiału ogniotrwałego, a następnie osuszany, aby utworzyć jednolitą powłokę powierzchniową zwaną „powłoką podstawową”. Na tym etapie osadza się bardzo drobne cząstki, tworząc cienką, ale bardzo gładką warstwę materiału inwestycyjnego, aby zapewnić gładką powierzchnię i skomplikowany szczegółowy produkt końcowy. Bardzo drobna krzemionka i inne spoiwa, w tym woda, krzemian etylu i kwasy są powszechnie stosowane jako materiały ogniotrwałe.
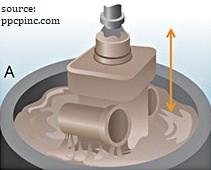
po wyschnięciu początkowej warstwy wzór jest wielokrotnie zanurzany i powlekany, aby zwiększyć jego grubość dla lepszej wytrzymałości. Ten drugi etap procesu zanurzania nazywa się” sztukaterią”, w której piasek lub inne kruszywo ogniotrwałe jest deszczowane na mokrą powierzchnię w celu zwiększenia grubości (5 do 15 mm ) i wytrzymałości.
czasami jako alternatywną metodę, pojedynczy klaster wzorcowy jest wstawiany do przepuszczalnej kolby do góry nogami i płynny materiał inwestycyjny wlewa się wokół niego. Kolba jest następnie wibrowana, aby usunąć uwięzione powietrze i upewnić się, że materiał inwestycyjny otacza wszystkie powierzchnie drzewa pleśni.
następnie pozostawia się go do całkowitego wyschnięcia, co może trwać od 16 do 48 godzin. Suszenie można przyspieszyć stosując podciśnienie lub minimalizując Wilgotność otoczenia.
Krok 6-Depilacja i Wypalanie
po całkowitym wyschnięciu i utwardzeniu formy materiału ogniotrwałego są one odwracane do góry nogami i umieszczane w piekarniku lub specjalnym autoklawie do depilacji, gdzie wosk może się stopić i wyczerpać (ryc. 7), a wszelkie późniejsze pozostałości odparowują. (Symulacje te pokazują, jak działają specjalistyczne Depilatory video 1 lub video 2)

usunięcie wosku wzorcowego z formy jest ważnym etapem w procesie odlewania inwestycyjnego, a nieprawidłowe wykonanie zmniejszy wydajność partii. Depilacja jest również jednym z głównych powodów pękania skorupy. Pękanie powłoki jest najczęstszą wadą odlewania.
Zasadniczo istnieją dwie główne metody usuwania woskowania, błyskawicznego ognia lub autoklawu (para wodna). Autoklawy parowe są preferowanym wyborem ze względu na równomierne ogrzewanie, które zmniejszyłoby nacisk na materiał.
forma jest podgrzewana (90oC–175oC) i utrzymywana w pozycji odwróconej przez kilka godzin (około 4 – 12 godzin), aby umożliwić stopienie się wosku i wyczerpanie się. Wosk wzorcowy jest zwykle odzyskiwany i poddawany recyklingowi. Następnie jest podgrzewany i utrzymywany w podwyższonej temperaturze (650oc–1095oc) przez kilka godzin (3-6 godzin), aby odpędzić wodę krystalizacji i spalić resztki wosku. Czas trwania i temperatury zależą od odlewanego metalu.
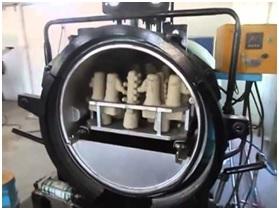
większość uszkodzeń powłoki występuje na etapie odparafinowania, ponieważ stosowane woski mają większy współczynnik rozszerzalności cieplnej niż materiał ogniotrwały. Dlatego wosk rozszerza się bardziej niż materiał inwestycyjny i wprowadza możliwe pękanie naprężeniowe na formie. Aby zmniejszyć ten efekt, wosk można szybko podgrzać, dzięki czemu zewnętrzny wosk topi się szybciej, a pozostały wosk rozszerza się bez obciążania formy. Autoklawy pokazane na fig. 8 są również używane do ogrzewania zmniejszającego ten efekt, ponieważ cykle ogrzewania mogą być bardziej jednolite i dokładniej kontrolowane.
Krok 7-Podgrzewanie & Odlewanie
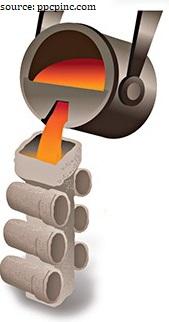
forma jest następnie wstępnie podgrzewana w przygotowaniu do nalewania. Podgrzewanie wstępne pozwala metalowi dłużej pozostać w stanie stopionym, dzięki czemu może lepiej wypełnić wszystkie szczegóły formy i zwiększyć dokładność wymiarową. Jeśli forma ostygnie, wszelkie znalezione pęknięcia można naprawić za pomocą zawiesiny ceramicznej lub specjalnego cementu. Ogrzewanie formy zapewnia również lepszą kontrolę wymiarową, ponieważ forma i metal mogą kurczyć się razem podczas chłodzenia.
stopiony metal do 3000oC wlewa się do wydrążonej formy, a następnie pozostawia do ostygnięcia. Podczas gdy odlewanie grawitacyjne jest najprostsze, można zastosować inne metody, aby zapewnić całkowite wypełnienie formy. W przypadku skomplikowanych, cienkich sekcji, napełnianie formy może być wspomagane przez dodatnie ciśnienie powietrza, odlewanie pochylone, odlewanie próżniowe lub proces odlewania odśrodkowego.
Krok 8-Knockout & post-processing
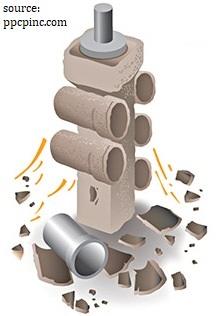
po zestaleniu się metalu stosuje się techniki takie jak odpryskiwanie mechaniczne, młotkowanie, wibracje, strumieniowanie wodą pod wysokim ciśnieniem i piaskowanie mediów w celu zerwania formy i usunięcia odlewu metalowego. Następnie poszczególne odlewy są odcinane, a nadmiar metalu usuwany. Wlew jest odcięty i w większości przypadków ponownie użyty. Część jest następnie przetwarzana zgodnie z wymaganiami produktu końcowego, takimi jak obróbka końcowa, obróbka cieplna, Obróbka powierzchni, malowanie itp.
- Kalpakjian, S., & Inżynieria Produkcji & Technologia (szósta edycja). Londyn: Pearson.
- Black, J. T, & Kohser, S. Ronald. (2012). Materiały & przetwarzanie w produkcji (jedenaste wydanie). Londyn: John Wiley.
- Beeley, Peter, (2009). Technologia odlewnicza (II wyd.). Oxford: Butterworth-Heinemann.
- Groover, P. Mikell, (2010). Podstawy nowoczesnej produkcji (IV wyd.). Oxford: John Wiley.